Friction reduced by 30%
Introduction
A customer was planning another well on the ongoing project. It was going to become the longest borehole on the field reaching 5,000 m MD and 4,024 m TVD by the first target T1, where 7” casing should have been set.
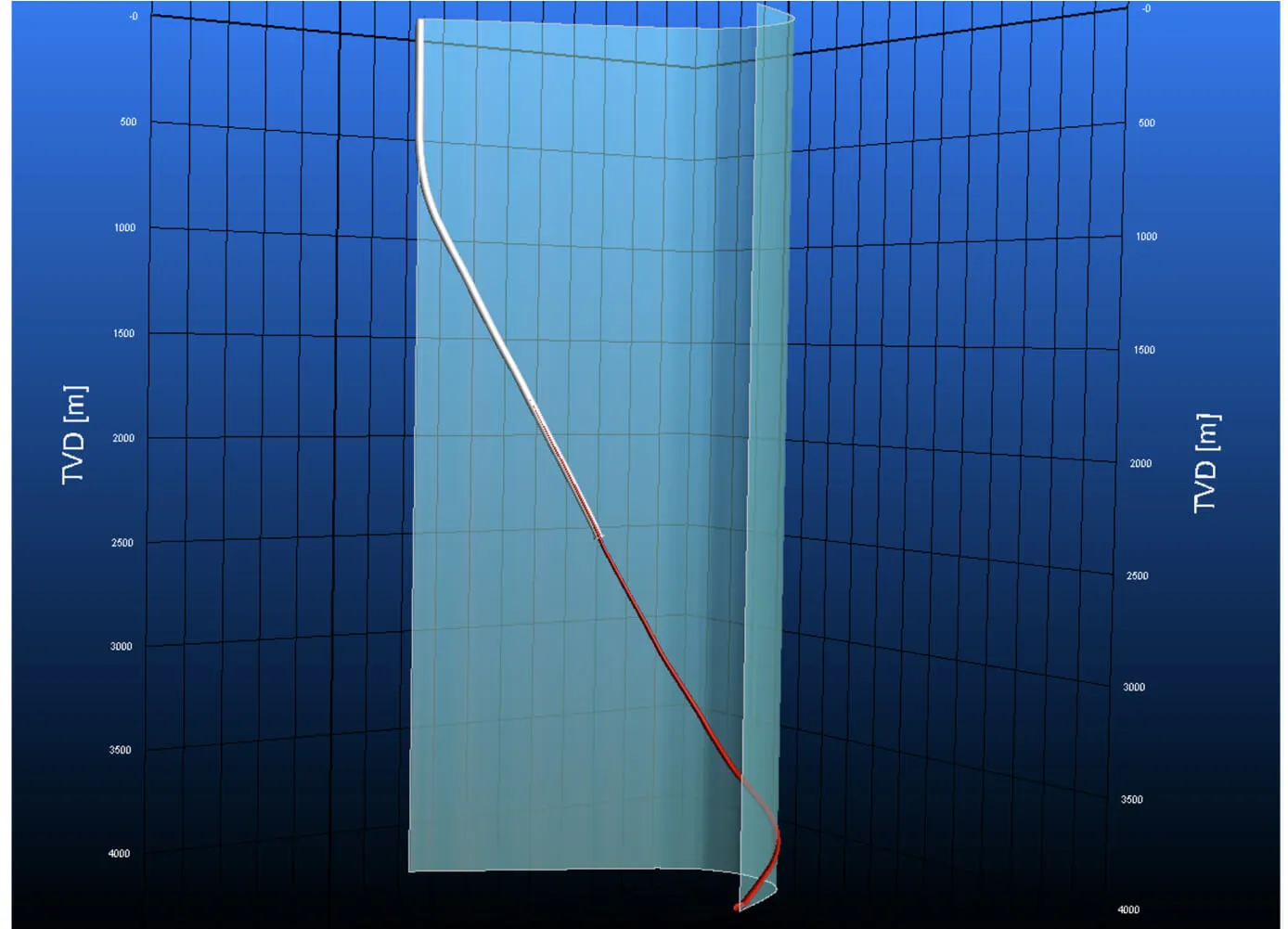
Customer challenge
A high-pressure formation at this depth requires thick wall casing of 32 ppf (48 kg/m) to withstand burst and collapse worst scenarios. Heavy joints combined with full-gauge bow-spring centralizers induce high tensile forces, so expected pick-up weights were exceeding safe yield limits with project history-based friction factors 0.22/0.28:
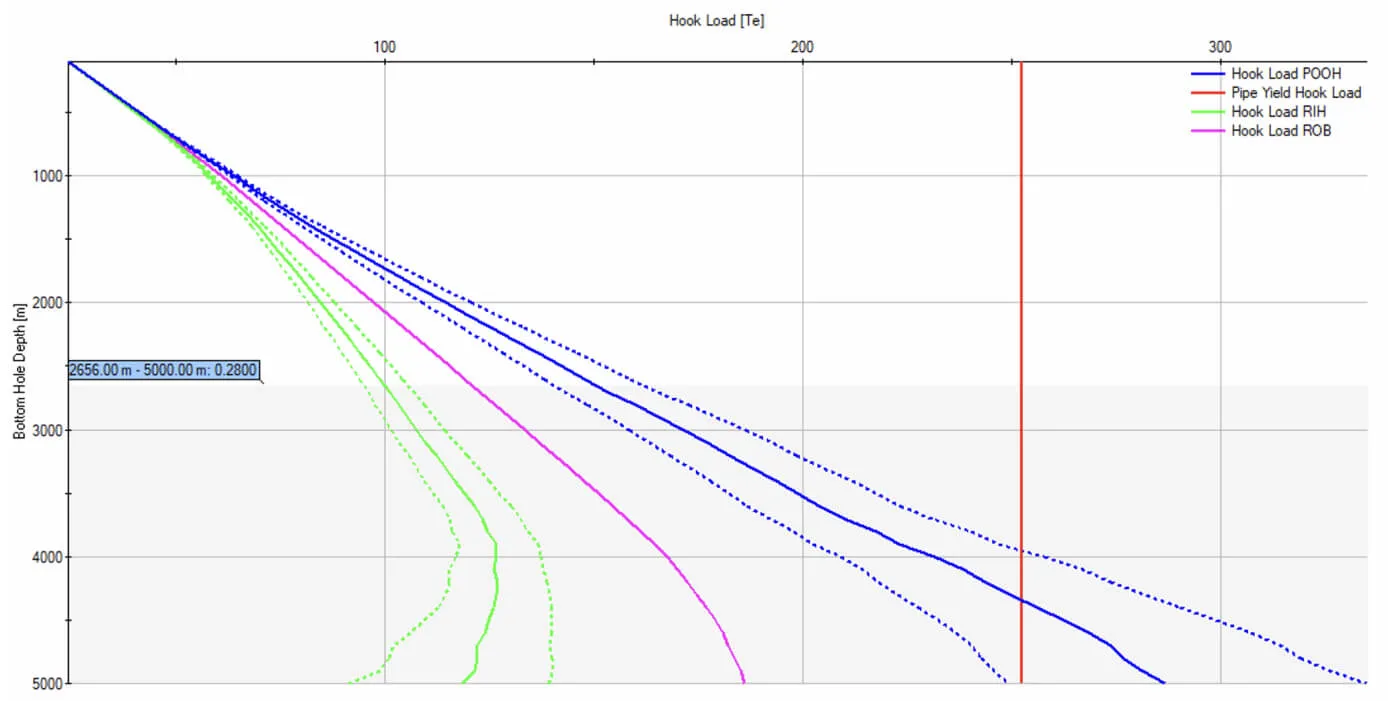
This was important issue for the client because at the very bottom of the section the unstable shale formation historically becomes a bottleneck for success. In case of a tight-spot, picking the casing up from this depth is essential for the safety of operation. Leaving swelling shales uncased may cause problems during drilling next horizontal section
Case Study Results
It was not easy to convince Client to increase number of centralizers and replace them with rigid under-gauge. Common sense advises that centralizers usually increase friction. But eliminating them completely was never an option because of high risk of differential stuck in permeable formations laid above.
Engineering calculations shows that despite reduced centralizer OD the average standoff is much better when placement frequency increased almost twice in open hole:
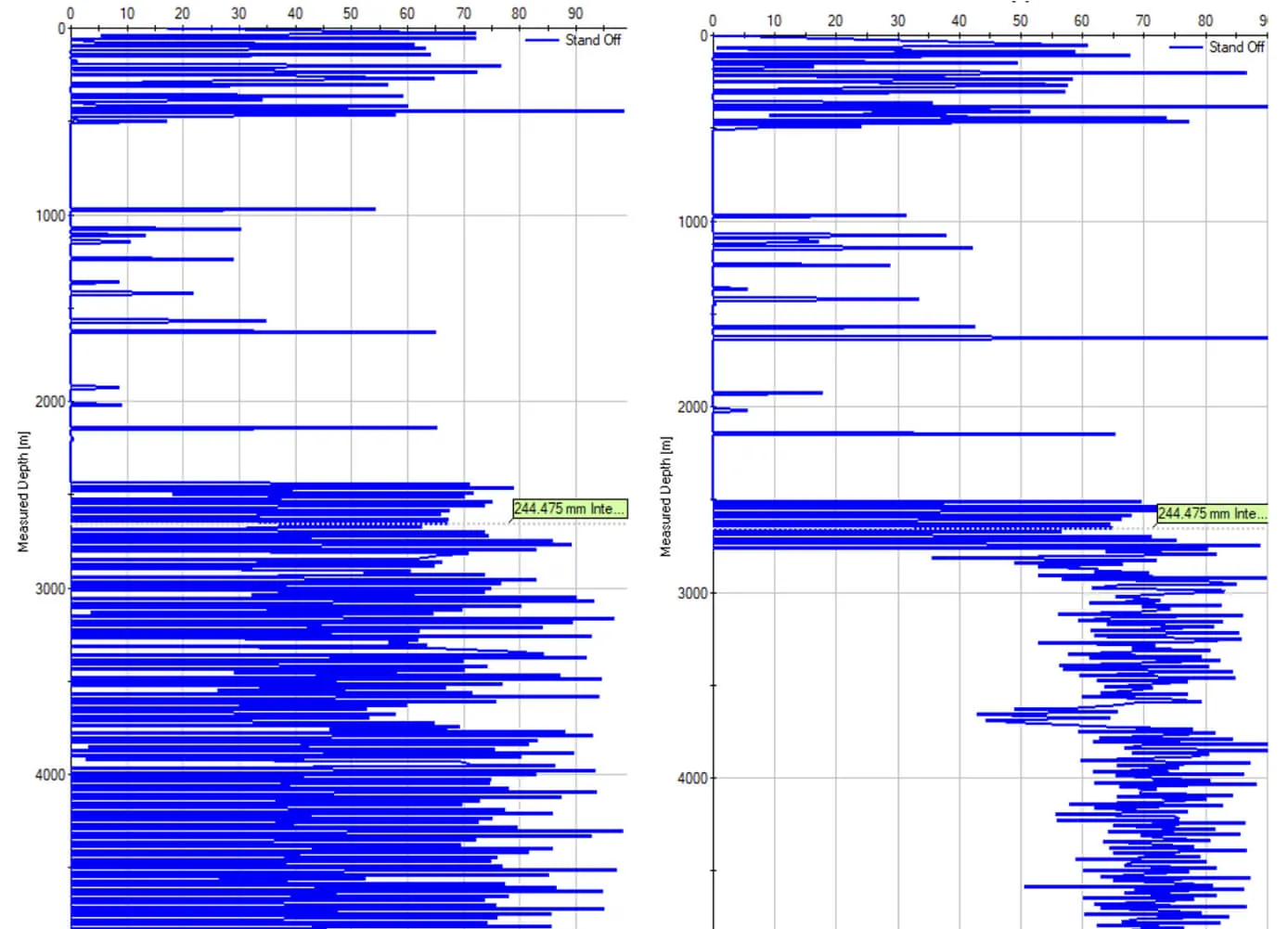
Centralizers producer claims friction coefficient below 0.1 with steel due to slick design and high-end material, which was not exactly confirmed while this casing run, however sufficient friction reduction clearly proven.
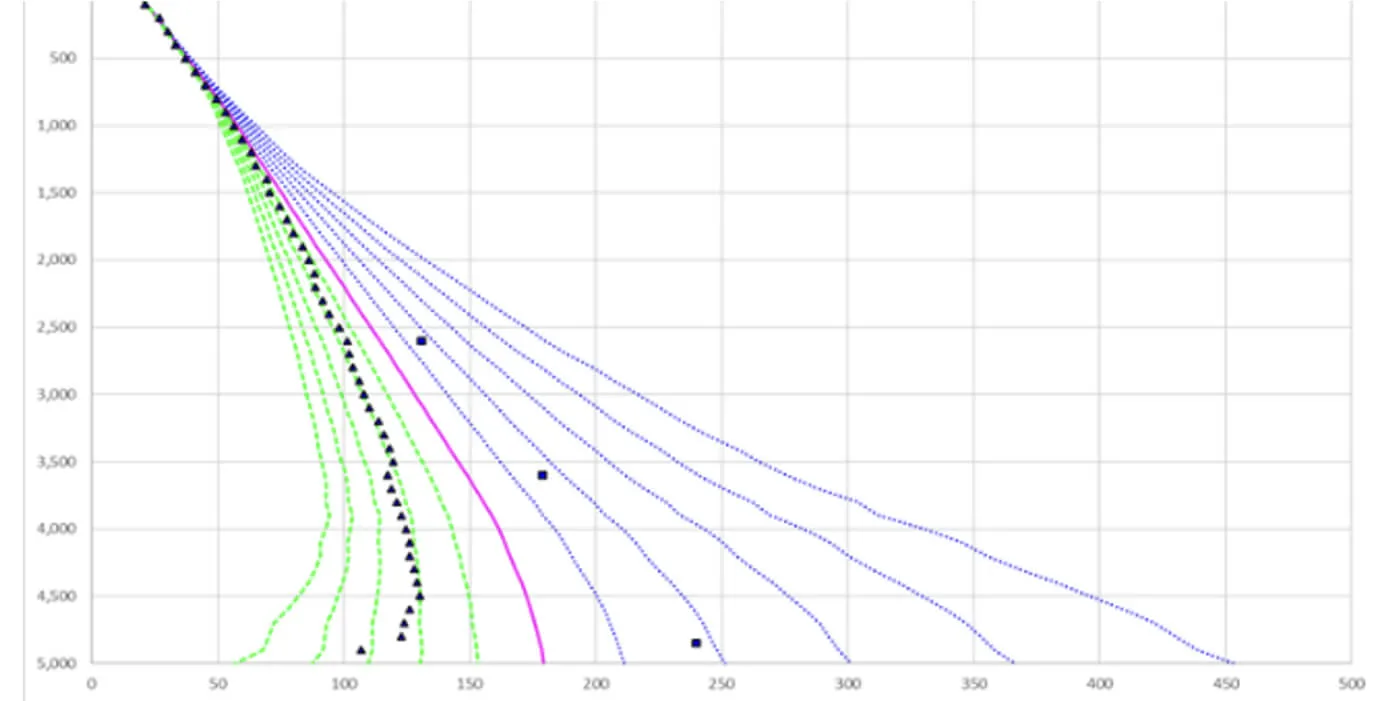
Customer Value
Overall drag reduction estimated by 30%, while formerly used bow-springs each required up to 150 kgf additional running force. Average stand-off increased from 0-90% up to 60-80% and mainly casing has been successfully set while being able to pick up for entire run.